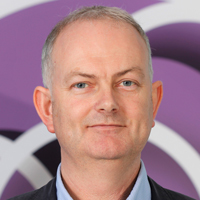
Barry Kennedy
CEO, Irish Manufacturing Research
Medical manufacturing is due a radical shift as a result of digitisation and new technology. Tech expert, Barry Kennedy, helps companies eliminate risk before they commit to big change.
How we live, learn, work and interact with each other have all been radically transformed by technology. Nowhere is that more apparent than in manufacturing where technology, is serving to disrupt traditional business models beyond all recognition.
Manufacturing companies need to ready themselves for further fundamental change, says Barry Kennedy, CEO of Irish Manufacturing Research:
Transformation at the scale of Airbnb and Uber
“In today’s world, businesses have to move quickly to stay ahead of competitors in order to gain an economic and global advantage.” Kennedy cites collaborative robotics, virtual reality, augmented reality, and the industrial internet of things as examples of developments likely to have the same impact on manufacturing at scales as big as, if not bigger than, what Airbnb and Uber had on the hospitality and taxi businesses.
Medical technology and biopharmaceuticals are two sectors that Kennedy and his team work with, to prepare companies for the big technological challenges that lie ahead. “Our role is to demystify and derisk new technologies for manufacturers, to ensure the Irish industry are resilient to the transformative changes that are coming.”
Medtech will be increasingly bespoke and customised
“When it comes to the medtech industry, the advent of customised medical devices means that the way these devices are made will be radically different in the very near future.”
Surgeons today have to manipulate a generic hip replacement so that it fits inside a patient’s body […] 3D printing will help create an exact replica of the patient’s original joint.
At their new 3D printing plant in Mullingar, medtech designers work in partnership with medical device companies, orthopaedic surgeons and clinicians to investigate the future production, for example bespoke artificial hip and knee joints for patients.
“Replacement hips and knees currently come in discrete sizes and surgeons today have to manipulate a generic part so that it fits inside a patient’s body,” Kennedy explains. “the future of this industry will involve 3D printing, where a surgeon will scan a patient’s joint and send it to be manufactured on one of these ground-breaking systems. This part will be an exact replica of the patients original one, which will result in less post-surgery recovery problems.
IMR, with its partner companies, such as Croom Medical Device or DePuy Synthes, are at the heart of the development of these breakthroughs.
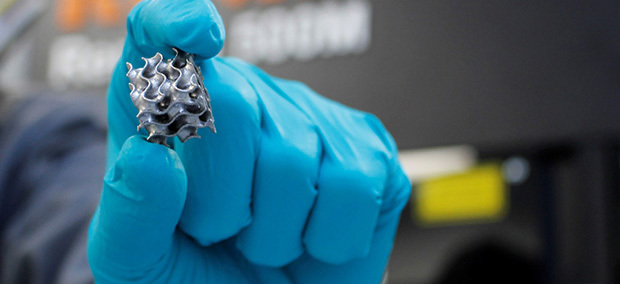
Technology will drive real-time, localised production
Digitisation and 3D printing will also require manufactures to make a fundamental shift in strategy, says Kennedy, with technology driving a move away from mass production to more just-in-time mass customisation (but with just the same efficiency as mass production).
“When it comes to medical devices, we could see a situation where production of parts will take place in smaller production units nearer to hospitals in a locality.”
Helping medtech manufacturers to stay ahead
“We undertake research that allows manufacturers to keep one step ahead,” Kennedy says of Irish Manufacturing Reseacch. “Advanced technology can be very expensive, so we have set up pilot lines and test beds for manufacturers to trial out these technologies before investing. We look at whether new systems or machinery are ready for mainstream manufacturing, and at what the machines are really capable of.”
We test if the technology is just hype, or if it’s truly a game-changer…
The research centre in Mullingar is a case in point. Home to leading edge 3D printing technology from leading companies such as Carbon 3D (a Silicon Valley-based company whose machines are being used to make for instance next generation customised soles for top-brand sports shoes). It houses a world-first, next-generation 3D printer from Renishaw, with which Irish Manufacturing Research are carrying out research for Croom Medical, in partnership with the SFI funded, I-Form Advanced Manufacturing Research Centre.
“Manufacturers are able to come along and work with the systems and our research team to test, trial, innovate, design, and deliver working products before investing in their own,” says Kennedy, in what he calls a ‘derisk’ approach. This suits manufacturers perfectly, as “together, we can all punch well above our weight.”
For more information about Irish Manufacturing Research, contact us on [email protected]