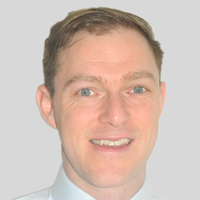
James Wall
Managing Director, 3D Technology Ireland
3D printing is quickly becoming an integral part of manufacturing in Ireland. The idea that ‘the technology is moving too fast to invest’ is nonsense and shouldn’t be intimidating to potential investors.
Take a car for example; a car today is slightly better than a similar car three years ago. But the fundamentals are still the exact same with some minor improvements – 3D printers are the same.
3D printing is ideal for low-volume, high-value items as well as bespoke consumer items and medical devices. With advances in software, medical device designers can now use real patient MRI data. We use this to produce a 3D-printed working model to help with the design of the medical or delivery device.
Case in point: injection moulding sees a 30% increase in efficiency with 3D printing solutions
Since the inception of industrial injection moulding, keeping an even temperature on the mould’s surface has been a constant challenge. However, 3D printing is helping to overcome this challenge; designing cooling channels, naturally following the contours of the part to be produced is now positioned as a modern solution. This has resulted in efficiency increases of up to 30%.
3D printing means medical implants can be bespoke to the individual
Surgeons benefit from individually designed hearing aids. This development means these fit perfectly and are patient specific.
Perfectly fitting implants deliver better surgical outcomes and recovery times, putting less of a burden on the HSE.
Digital moulding to replace injection moulding
Digital moulding is now becoming a new era for manufacturing. As an industry, 3D printing is seeking to disrupt industrial production practices that have been dominated by injection moulding for over a century.
Today, we are closer than ever to that reality: sophisticated 3D printing technologies are proving to be a viable means for fulfilling new manufacturing philosophies centred on quick turnarounds and smaller-volume production.
Automated parts production is cheaper for manufacturers
The 3D technology for this application uses a series of connected print engine modules integrated with an automated robotics system to continuously produce plastic parts quickly and efficiently – enabling tool-less digital moulding.
By eliminating tooling requirements and speeding up the time to market, digital moulding using 3D printing also offers cost advantages to manufacturers. Notably, by eliminating various manufacturing steps associated with traditional manufacturing, digital moulding delivers reduced labour, machining, iteration and testing costs.
Large furniture retailers using 3D printing to create customers’ unique designs
Large retailers are now looking at bringing bespoke consumer products in-house for sale. This means3D printing is perfect for innovative design, allowing designers full freedom when creating their products and giving the consumer a bespoke product that differs from anything else in the market. We are also now seeing this adoption with large furniture retailers.
3D printing is allowing industry to create intricate designs that are immediately manufacturable. It is delivering lightweight parts for aircraft that meet or exceed weight to strength requirements and increase the speed of product design and production from months to days. Conclusively, it is an exciting opportunity, and very much worth investing in, today.