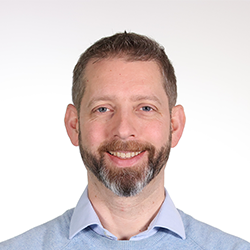
Colin Meade
Additive Manufacturing Technologist, Irish Manufacturing Research
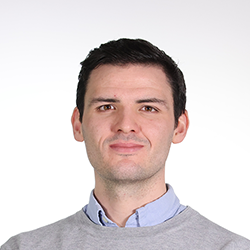
Mark Hartnett
Additive Manufacturing Senior Technologist, Irish Manufacturing Research
The digital design freedom inherent in Additive Manufacturing, when applied to the production of tool steel moulds, opens up new boundaries of controlled cooling.
Additive Manufacturing (AM), or 3D Printing, unlocks the potential to create highly complex three-dimensional designs which are not easily possible with conventional manufacturing processes. This opens up new possibilities in design complexity and precision.
Additive Manufacturing efficiencies
AM can be a tool for efficiency. It allows for complex internal channels, creating winding paths with unprecedented ease. One of the most effective ways to implement this is to use it for optimising cooling paths within tooling, integral to Injection Moulding.
This optimisation, known as Conformal Cooling, closely aligns the cooling line with the cavity, significantly improving cooling, reducing cycle times and enhancing the overall sustainability of the process. As AM is fundamentally a digital workflow, applying a simulation-led design process is straightforward and can significantly de-risk the entire operation.
Conformal Cooling is fast
The demand for greater production flexibility has never been higher, and Conformal Cooling is answering this call. It has revolutionised tooling, often reducing mould cycle times by over 30%. Manufacturers can utilise cooling with precision, ensuring efficiency where it matters most.
Internationally, AM is gaining traction, with many competitors employing this technology to stay ahead.
Environmental impact and global competitiveness
AM extends beyond efficiency; it’s a path to environmental responsibility. By optimising tool cooling, significant energy savings are realised, reducing the reliance on chilled water systems. This not only offers substantial cost savings but also lessens the environmental footprint of injection moulding.
Internationally, AM is gaining traction, with many competitors employing this technology to stay ahead. Irish firms, known for their emphasis on quality over cost, are recognising that AM is the key to remaining competitive in a rapidly evolving market and have observed a notable trend: their competitors are consistently quoting significantly reduced cycle times.
The key to this efficiency? Additive Manufacturing, specifically its application in creating conformally cooled tooling, is the driving force behind these impressive time reductions. Employing cutting-edge industrial AM capability at its Mullingar pilot factory, Irish Manufacturing Research (IMR) has successfully delivered an end-to-end production capability in Conformal Cooling for Irish injection moulding companies.
A large consumer manufacturer attests to the effectiveness of AM, stating: “For the past decade, we’ve employed AM in every tool we’ve made; we are the best in the world at it.”
Why it’s also about quality
In economies with high production costs, like Ireland, AM’s value extends beyond speed. It’s about meeting stringent quality standards and handling complex designs and materials. AM offers a solution — facilitating faster production while ensuring deeper cooling penetration into the tool. This results in deeper process control and a more balanced thermal system, leading to better quality parts and significantly reducing defects and waste.